4 Key Kpis to Prioritize in Supply Chain Logistics
Navigating the complexities of supply chain logistics requires a strategic focus on key performance indicators (KPIs). This article distills expert insights into the most crucial KPIs to prioritize for operational success. Learn how to effectively monitor and enhance your supply chain's performance from industry leaders.
- Monitor Freight Cost Percentage
- Prioritize On-Time Delivery Rate
- Ensure On-Time Delivery
- Track On-Time Delivery Rate
Monitor Freight Cost Percentage
At Transport Works we thrive on analytics. We produce KPI reporting for all our customers and one of the most important and reliable metric we measure is freight cost as a % of sale. We monitor the % and any movement up or down is investigated. Another metric we monitor is DIFOT (Delivery In Full & On Time). The reason this is just as important is with a higher on time delivery performance, our clients customers have a better purchasing experience and this in turn leads to repeat business.
Prioritize On-Time Delivery Rate
One critical KPI I prioritize in supply chain logistics is On-Time Delivery Rate (OTDR), which measures the percentage of shipments delivered within the promised timeframe. This metric is vital to our business for several reasons: First, it directly impacts customer satisfaction and retention. When we consistently meet delivery promises, we build trust and strengthen relationships with our clients. Late deliveries can lead to production delays for our customers and damage our reputation. Second, OTDR helps us identify inefficiencies in our supply chain. By tracking this metric, we can pinpoint bottlenecks, whether they're in warehousing, transportation, or last-mile delivery. For example, if we notice a drop in on-time deliveries in a specific region, we can investigate the root causes and implement targeted improvements. Finally, maintaining a high OTDR helps control costs. Late deliveries often result in expedited shipping charges, overtime labor costs, and potential penalties or chargebacks from customers. By monitoring and optimizing this KPI, we protect our profit margins while delivering better service.
Ensure On-Time Delivery
On-time delivery (OTD) is the holy grail of supply chain KPIs. It's the ultimate measure of whether your logistics are running like a well-oiled machine. Why does it matter? Late deliveries don't just annoy customers-they cost you in lost trust, missed revenue, and potential churn. Prioritizing OTD ensures we're meeting expectations and keeping the whole system-from suppliers to customers-running smoothly. It's not just a metric; it's a trust-builder.
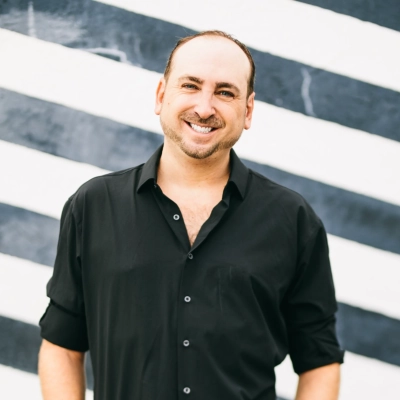
Track On-Time Delivery Rate
One key performance indicator (KPI) I prioritize in supply chain logistics is on-time delivery rate. This metric is crucial because it directly impacts customer satisfaction, retention, and brand reputation. If we consistently deliver products on time, customers are more likely to return for future purchases and recommend our services to others. Delays, on the other hand, can lead to customer frustration, increased returns, or even loss of business.
By monitoring on-time delivery, we can identify inefficiencies in the supply chain, whether it's with inventory management, transportation, or vendor performance. This KPI allows us to make data-driven decisions to optimize routes, improve warehouse operations, or negotiate better terms with suppliers to ensure timely delivery. Keeping this metric high is essential for maintaining a reliable service, reducing costs associated with delays, and ultimately supporting long-term business growth.
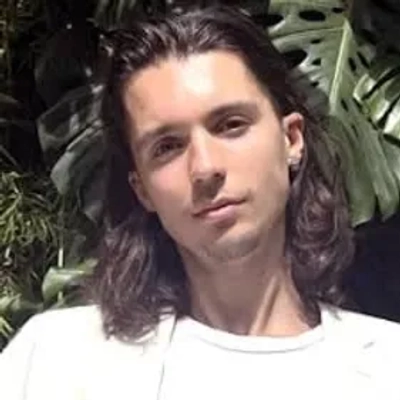