5 Technology Solutions that Boost Warehouse Efficiency
Discover the technology solutions that are revolutionizing warehouse efficiency. This article delves into expert insights on how modern tools like Multipick, advanced Warehouse Management Systems (WMS), and automation are transforming operations. Gain a competitive edge with strategies that reduce errors and enhance real-time inventory tracking.
- Switching To Multipick Fixed All Our Issues
- Automation Rules In Presorting And Organizing Orders
- Advanced WMS Transformed Our Operations
- WMS And Real-Time Inventory Tracking Improved Efficiency
- WMS And Barcode Scanning Reduced Errors
Switching To Multipick Fixed All Our Issues
Partnering with the right WMS (Warehouse Management System) is key to the success of any warehouse. We have partnered with a company called Interlogic and their WMS Multipick. Our previous QMD platform did not have an address validation feature and this caused a huge breakdown in order processing and flow. Switching to Multipick and their address validation tool fixed all our issues and has got our customers back on track and orders flowing seamlessly once again. As well as address validation, Multipick has a suite of features including local carrier integrations, seamless integrations with well known ERP's and being cloud based.
Automation Rules In Presorting And Organizing Orders
Automation rules in presorting and organizing orders in mass. In an organization that had 3k+ SKUs trying to find harmony in the chaos came down to organizing the orders by similar products and location. Due to the nature of the product it was all very contained to a small space. We found that grouping our orders based on what made up the order became the best way. A solid ERP/WMS made the difference. For us it was Fulfil.io.
Advanced WMS Transformed Our Operations
At Delta Fulfillment, we've implemented an advanced warehouse management system that's transformed our operations from good to great. This technology means we always know exactly what's in stock and where to find it, ensuring 99.92% of orders ship within SLA. It also has improved our pick and pack accuracy rate to 99.85%, which means customers get exactly what they ordered, every time.
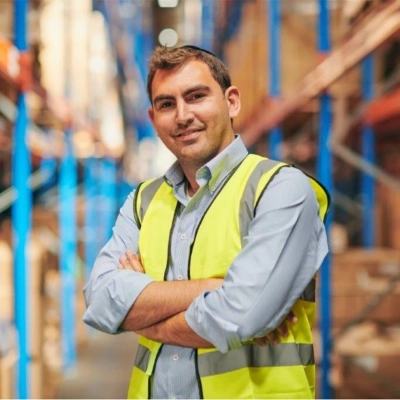
WMS And Real-Time Inventory Tracking Improved Efficiency
One example of how I leveraged technology to improve warehouse efficiency was by implementing a warehouse management system (WMS) paired with real-time inventory tracking.
Before, we relied on manual processes for inventory counts and order fulfillment, which often led to delays and errors. I introduced the WMS to automate much of this, allowing us to track inventory in real-time and dynamically allocate stock based on order priority. We also integrated barcode scanning technology to streamline picking and packing, reducing human error and speeding up the process.
The results were significant: we reduced order fulfillment time by 25%, and our error rate dropped by over 30%. The system also provided valuable data insights, allowing us to forecast demand more accurately and optimize stock levels, ultimately improving our ability to meet customer needs faster and more efficiently. This technology has been key in scaling our operations while maintaining high service quality.
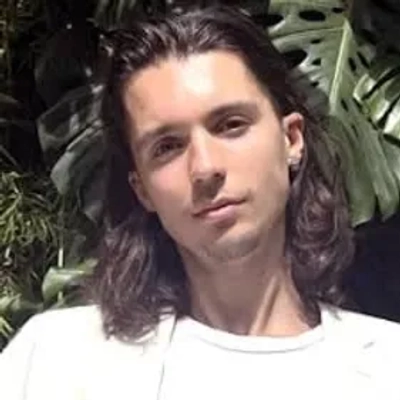
WMS And Barcode Scanning Reduced Errors
At Tech Advisors, we believe in using technology to solve real-world problems for businesses. One example is when we helped a client struggling with warehouse inefficiencies and frequent order fulfillment errors. Their manual inventory tracking process led to stock discrepancies, delays, and misplaced items. To fix this, we implemented a Warehouse Management System (WMS) with barcode scanning technology, which allowed real-time tracking of inventory locations and reduced human errors in the picking process.
With barcode scanning, workers could instantly verify the correct items while picking orders, preventing costly mistakes. The WMS also optimized picking routes, reducing unnecessary travel time and making the workflow more efficient. As a result, the client saw a noticeable improvement in order accuracy and faster fulfillment times, helping them keep up with customer demands without added labor costs.
This experience reinforced the importance of automation in warehouse management. Businesses dealing with inventory challenges should consider systems that provide real-time data access and reduce reliance on manual processes. Investing in the right tools not only improves accuracy, but also boosts productivity, allowing teams to focus on higher-value tasks instead of fixing preventable errors.