7 Lessons from Supply Chain Failures and Setbacks
Supply chain failures and setbacks can have far-reaching consequences for businesses across industries. This article delves into valuable lessons learned from past supply chain disruptions, offering insights from seasoned experts in the field. Discover practical strategies for strengthening your supply chain, from implementing robust risk assessment to fostering collaborative supplier relationships.
- Due Diligence Prevents Supply Chain Collapse
- Diversify Suppliers and Build Contingency Plans
- Spread Risk Through Supply Chain Diversification
- Leverage Real-Time Visibility for Proactive Solutions
- Prioritize Supplier Agility Over Cost Alone
- Implement Robust Risk Assessment Strategies
- Foster Collaborative Relationships with Key Suppliers
Due Diligence Prevents Supply Chain Collapse
One of the most impactful lessons I've learned came from my early days as an ecommerce business owner, before founding Fulfill.com. I had spent months growing my brand to a 7-figure operation, only to have it nearly collapse because I partnered with the wrong 3PL provider.
This particular fulfillment center promised everything – competitive rates, fast shipping, excellent inventory management – but the reality was dramatically different. Orders were shipped late or to incorrect addresses, inventory counts were consistently wrong, and customer service was non-existent. Our customer complaints skyrocketed and sales plummeted. We were hemorrhaging money and reputation simultaneously.
The painful lesson? Due diligence isn't just a buzzword – it's survival. I had selected this provider based primarily on cost and proximity, without thoroughly investigating their operational capabilities or speaking with existing clients. I hadn't asked the right questions or demanded proof of performance.
This experience fundamentally shaped how we've built Fulfill.com. Now, we conduct exhaustive vetting of every 3PL in our network, including surprise facility visits, multiple client references, and comprehensive capability assessments. We evaluate providers not just on what they promise but on their demonstrated ability to execute consistently.
When I work with ecommerce brands today, I emphasize that choosing a fulfillment partner isn't just a vendor decision – it's a strategic partnership that can determine your company's fate. The cheapest option is rarely the best value, and the true cost of poor fulfillment extends far beyond operational inefficiencies to impact customer lifetime value and brand reputation.
This lesson has also made me a stronger advocate for transparency in the logistics industry. The old model of obscuring capabilities and costs behind complex contracts simply doesn't serve modern ecommerce businesses. What matters is finding the right operational fit for your specific needs, and that requires honest conversation from the beginning.
Diversify Suppliers and Build Contingency Plans
One key lesson I learned from a supply chain setback was the importance of building stronger relationships with suppliers. During a previous project, a key supplier failed to deliver on time, which caused significant delays and impacted customer satisfaction. After that experience, I shifted my approach by diversifying our supplier base and establishing clearer communication channels. I also worked on building contingency plans for future disruptions, ensuring we had backup options in place. This proactive approach allowed us to handle unexpected delays much better in the future, minimizing the impact on the business. What I've learned is that supply chain resilience isn't just about having a Plan B—it's about having solid, transparent relationships and being ready to pivot quickly when challenges arise.
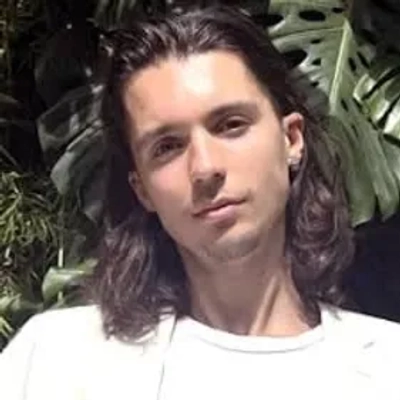
Spread Risk Through Supply Chain Diversification
Supply chain diversification is a crucial lesson learned from failures and setbacks. Relying on a single supplier or source can leave businesses vulnerable to disruptions. By spreading out supply sources, companies can reduce the risk of complete operational halts due to unforeseen circumstances.
This approach ensures that if one supplier faces issues, others can still provide necessary materials or services. Diversification also opens up opportunities for cost savings and improved quality through healthy competition among suppliers. Companies should evaluate their current supply chain and identify areas where diversification can be implemented to increase resilience.
Leverage Real-Time Visibility for Proactive Solutions
Real-time visibility across supply networks has become an essential tool for preventing and managing supply chain failures. Modern technology allows companies to track shipments, inventory levels, and production status in real-time. This information enables quick decision-making and proactive problem-solving when issues arise.
With comprehensive visibility, businesses can identify potential bottlenecks or disruptions before they escalate into major problems. It also helps in maintaining accurate inventory levels and improving overall efficiency. Organizations should invest in advanced tracking systems and data analytics to gain better insights into their supply chain operations.
Prioritize Supplier Agility Over Cost Alone
When selecting suppliers, prioritizing agility over cost can lead to a more robust supply chain. While cost-cutting is important, choosing suppliers solely based on price can result in inflexibility during crises. Agile suppliers can quickly adapt to changing circumstances, alter production methods, or find alternative solutions when faced with challenges.
This flexibility can be the difference between a minor hiccup and a major supply chain breakdown. Agility also often translates to better quality and innovation, as these suppliers are more likely to stay updated with industry trends and technologies. Businesses should reassess their supplier selection criteria to give more weight to agility and adaptability.
Implement Robust Risk Assessment Strategies
Implementing robust risk assessment and mitigation strategies is crucial for preventing supply chain setbacks. This involves identifying potential risks at every stage of the supply chain and developing plans to address them. Regular audits, scenario planning, and stress testing can help uncover vulnerabilities before they become problems.
Effective risk management also includes having contingency plans for various potential disruptions, from natural disasters to geopolitical issues. By being proactive rather than reactive, companies can minimize the impact of supply chain failures. Organizations should establish a dedicated team or process for ongoing risk assessment and mitigation planning.
Foster Collaborative Relationships with Key Suppliers
Developing strong collaborative relationships with key suppliers can significantly reduce the likelihood of supply chain failures. These partnerships go beyond transactional interactions, involving shared goals, open communication, and mutual support. Collaborative relationships enable better forecasting, joint problem-solving, and shared innovation.
When challenges arise, strong partnerships can lead to quicker resolutions and more creative solutions. This approach also tends to result in higher quality products and services, as suppliers are more invested in the success of their partners. Companies should identify their most critical suppliers and work on building deeper, more collaborative relationships with them.