What’s a Cost-Saving Measure You’ve Found Effective in Procurement Without Compromising on Quality?
Operations managers are constantly balancing the scales of cost and quality, seeking innovative strategies to save without sacrifice. From a National Supply Chain Manager's perspective on prioritizing long-term quality, to the additional five answers including the implementation of Just-In-Time inventory systems, we've gathered a spectrum of effective cost-saving measures. These insights come from industry veterans and seasoned professionals, offering a blend of expertise and practical approaches to procurement efficiency.
- Prioritize Long-Term Quality Over Price
- Secure Bulk Discounts Without Quality Loss
- Form Cost-Quality Strategic Supplier Partnerships
- Optimize Inventory with Technology
- Lock in Prices with Multi-Year Contracts
- Invest in Energy-Efficient Manufacturing
- Implement Just-In-Time Inventory Systems
Prioritize Long-Term Quality Over Price
When it comes to cost savings in procurement, my perspective is somewhat unconventional. Often, sourcing something advertised and offered at the 'lowest price around' may provide initial savings but risk future incurred costs, contributing to the overall spend if the quality is not up to standards. Evaluating what is important to your operations and taking pride in the quality of your item or finished goods may actually mean purchasing at a competitive market price, with the reassurance that you are receiving a reliable, quality product. In the long term, this will actually provide you with not only savings on the product but also productivity. It is best to examine the overall operational needs and assess risks with cost savings in advance. Alternatively, savings can be explored in other areas such as freight and delivery.
Secure Bulk Discounts Without Quality Loss
Negotiating bulk discounts with suppliers has proven to be an effective cost-saving measure. At Sartoro, we achieved significant savings by consolidating our fabric orders to reach minimum order thresholds, allowing us to secure lower prices per unit while maintaining quality. By accurately forecasting demand and analyzing purchasing patterns, we negotiated better terms and reduced overall costs. This approach cut expenses and streamlined our supply chain, balancing financial efficiency with product excellence. It's a strategy that keeps costs down without compromising on the quality of what we deliver.
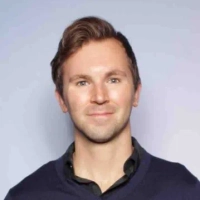
Form Cost-Quality Strategic Supplier Partnerships
Forming strategic partnerships with suppliers can lead to significant savings and the potential for improving quality through the sharing of best practices. By working closely with suppliers to develop products that meet both cost and quality targets, organizations can often gain access to newer, more cost-effective materials and innovations. Such partnerships may include collaborative planning and forecasting, which can streamline processes and reduce waste.
A concentrated effort towards mutual success fosters a relationship where suppliers are more likely to invest in quality improvements that benefit both parties. Explore opportunities to create a strategic alliance with a key supplier that will drive down costs while maintaining the high standards of quality you require.
Optimize Inventory with Technology
Utilizing modern technology to manage inventory can drastically reduce costs by optimizing stock levels and minimizing excess. Efficient inventory management software can forecast demand using data analytics, which allows companies to have the right amount of stock at the right time, avoiding both overstock and stockout situations. This balance not only saves on storage and insurance costs but also ensures that quality products can be delivered to customers in a timely manner.
Embracing technology in inventory management also minimizes human error, leading to more accurate ordering processes. Investigate and invest in an inventory management system that can refine your procurement processes, aligning cost savings with quality assurance.
Lock in Prices with Multi-Year Contracts
Negotiating multi-year contracts with suppliers can provide a stable source of quality materials at discounted rates. Suppliers are often willing to offer lower prices in exchange for the guarantee of a long-term relationship, which provides them with predictability and reduces their marketing and sales costs. This approach can also lock in prices, helping to protect the buyer from market volatility and price spikes.
Consistent pricing over several years enables more accurate budgeting and financial planning. Begin discussions with suppliers to secure a multi-year agreement that offers both better rates and sustained quality.
Invest in Energy-Efficient Manufacturing
Incorporating energy-efficient technologies and practices into manufacturing processes can lead to substantial cost reductions without cutting corners on quality. By using less energy, companies not only lower their utility bills but also often find that the more efficient equipment and processes produce less waste and maintain or improve the quality of the final product.
Additionally, energy efficiency can contribute to a company's sustainability goals, which can enhance brand image and customer loyalty. Assess your current manufacturing processes and pinpoint areas where energy efficiency improvements can be made to save costs and potentially increase quality.
Implement Just-In-Time Inventory Systems
Adopting a just-in-time (JIT) inventory system can significantly cut costs by minimizing the amount of inventory kept on hand. This method relies on precise scheduling and timely delivery of materials to align closely with production schedules. It reduces the costs associated with warehousing, including rent, utilities, and staffing, while also minimizing the risk of inventory obsolescence.
By receiving goods only as they are needed, companies can ensure that they are using the freshest materials possible, thereby supporting quality. Consider shifting to a JIT inventory system to control costs and potentially enhance the quality of your products or services.